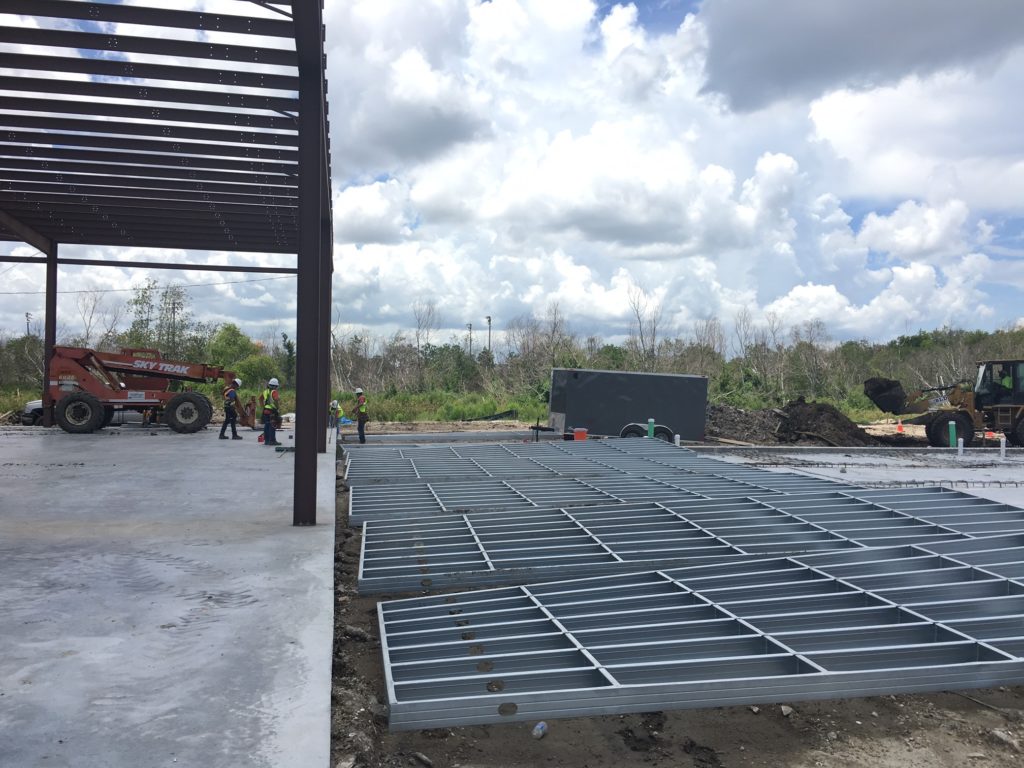
In construction, the choice of building materials plays a critical role in the strength, durability, sustainability, and cost of a project. Two of the most common framing materials are light gauge steel (LGS), exemplified by Strukko StandFast® Light Gauge Steel Frames, and traditional wood framing. Both materials have their unique advantages and disadvantages, making them suited to different types of projects. This article provides a detailed comparison of Strukko StandFast® LGS frames and traditional wood framing, evaluating their pros, cons, and best uses.
Strukko StandFast® Light Gauge Steel Frames
Pros
1. Strength and Durability
One of the biggest advantages of Strukko StandFast® LGS frames is their superior strength and durability. Steel offers a high strength-to-weight ratio, meaning it can bear heavy loads without requiring a significant amount of material. This makes LGS framing ideal for multi-story buildings, long-span structures, and applications requiring high structural integrity.
2. Fire Resistance
Unlike wood, steel does not burn. LGS frames offer superior fire resistance, which can enhance the safety of buildings and reduce insurance premiums. This makes it particularly valuable for buildings in areas with higher fire risks.
3. Pest and Rot Resistance
Steel is immune to termites, mold, and rot, problems that commonly affect wooden structures. Buildings framed with LGS have a longer lifespan in environments where wood may deteriorate due to moisture or pests, such as coastal regions or humid climates.
4. Precision and Waste Reduction
LGS frames are typically prefabricated with precision in a controlled factory environment. This reduces construction waste on-site, shortens build times, and ensures accurate and consistent framing. Prefabrication also minimizes human error during installation, improving overall building quality.
5. Recyclability and Sustainability
Steel is highly recyclable. At the end of its life cycle, Strukko StandFast® LGS frames can be fully recycled without any degradation of quality. This contributes to more sustainable construction practices and helps reduce the environmental impact of the building industry.
Cons
1. Thermal Conductivity
Steel is a highly conductive material, which can lead to thermal bridging—where heat is transferred through the metal from one side of the wall to the other. This can reduce a building’s overall energy efficiency unless appropriate insulation techniques are applied.
2. Higher Material Costs
Although steel prices fluctuate, LGS frames can be more expensive than wood in terms of raw materials. However, the reduced labor costs and shorter construction times can sometimes offset the initial expense.
3. Limited Availability of Contractors
Wood framing is more familiar to many contractors, particularly in residential construction. Finding skilled laborers experienced in LGS framing may be more challenging in certain regions, which could impact project timelines and costs.
Traditional Wood Framing
Pros
1. Lower Material Costs
Wood framing is generally less expensive than steel in terms of raw materials, making it an attractive option for residential construction, especially for smaller-scale projects or those with tight budgets.
2. Widespread Availability and Familiarity
Wood framing is the traditional standard in residential construction, particularly in North America. There is a large pool of contractors who are experienced in wood construction, and the materials are widely available, making it easier to start and complete projects efficiently.
3. Thermal Performance
Wood is a natural insulator and does not conduct heat as readily as steel. This reduces the risk of thermal bridging, making wood-framed buildings inherently more energy-efficient without the need for additional insulation measures.
4. Ease of Modification
Wood framing is relatively easy to cut, adjust, and modify during construction. If changes are needed on-site, contractors can quickly adapt without requiring specialized tools or significant additional costs.
Cons
1. Vulnerability to Pests and Decay
One of the major drawbacks of wood framing is its susceptibility to pests like termites, as well as rot and mold in damp conditions. This can lead to structural problems over time, particularly in regions with high moisture or pest activity.
2. Fire Risk
Wood is highly combustible, increasing the risk of fire damage in buildings constructed with traditional wood framing. This can also raise insurance costs and necessitate additional fireproofing measures.
3. Structural Limitations
While wood is strong, it doesn’t have the same strength-to-weight ratio as steel. Wood framing is less suited to multi-story or long-span structures, as it may require additional support systems that can increase costs and complexity.
4. Sustainability Concerns
Although wood is a renewable resource, deforestation and irresponsible logging practices have raised concerns about the long-term sustainability of wood framing. Sustainable wood sourcing and certifications like FSC (Forest Stewardship Council) can help mitigate these issues, but they may increase costs.
Best Uses: Strukko StandFast® LGS Frames vs. Traditional Wood Framing
Best Uses for Strukko StandFast® LGS Frames
- Commercial and Industrial Buildings: The strength and durability of LGS frames make them ideal for larger structures like warehouses, retail spaces, and multi-story office buildings.
- Multi-Story Residential Construction: For mid-rise apartments, condominiums, and mixed-use buildings, LGS provides the necessary structural support while being lighter than traditional materials like concrete.
- Areas with High Fire Risk: Buildings in regions prone to wildfires benefit from LGS frames due to their non-combustible nature.
- Coastal and Humid Environments: The resistance of steel to moisture and pests makes it perfect for construction in coastal areas, flood zones, and humid climates where wood may deteriorate over time.
- Sustainable and Recyclable Projects: LGS framing is well-suited for projects with a strong emphasis on sustainability and eco-friendliness due to its recyclability and reduced waste during construction.
Best Uses for Traditional Wood Framing
- Single-Family Homes: For smaller-scale residential projects, wood framing is often more economical and easier to work with, especially in areas where wood is abundant and labor costs are lower.
- Renovations and Additions: Wood framing is ideal for renovations and home additions, as it can be easily modified and adapted on-site, even during construction.
- Regions with Temperate Climates: In areas with low humidity and minimal pest activity, wood can last for decades with minimal issues, making it a practical choice for residential construction.
- Projects with Tight Budgets: For builders working within a limited budget, wood framing is typically more cost-effective, especially for smaller or less complex structures.
Conclusion
Both Strukko StandFast® Light Gauge Steel Frames and traditional wood framing have their merits, and the choice between the two ultimately depends on the specific requirements of the project. LGS frames offer superior strength, durability, and sustainability, making them ideal for commercial, multi-story, and eco-conscious construction projects. On the other hand, traditional wood framing remains a popular choice for residential construction due to its lower cost, ease of use, and widespread availability.
Understanding the strengths and limitations of each material helps builders and architects make informed decisions, ensuring that the framing system they choose is the best fit for their project’s goals, budget, and environmental conditions.